Porosity in Welding: Identifying Common Issues and Implementing Ideal Practices for Avoidance
Porosity in welding is a prevalent issue that frequently goes undetected until it creates considerable issues with the stability of welds. In this discussion, we will certainly explore the essential aspects adding to porosity formation, examine its damaging effects on weld performance, and review the best techniques that can be taken on to lessen porosity event in welding processes.
Common Root Causes Of Porosity
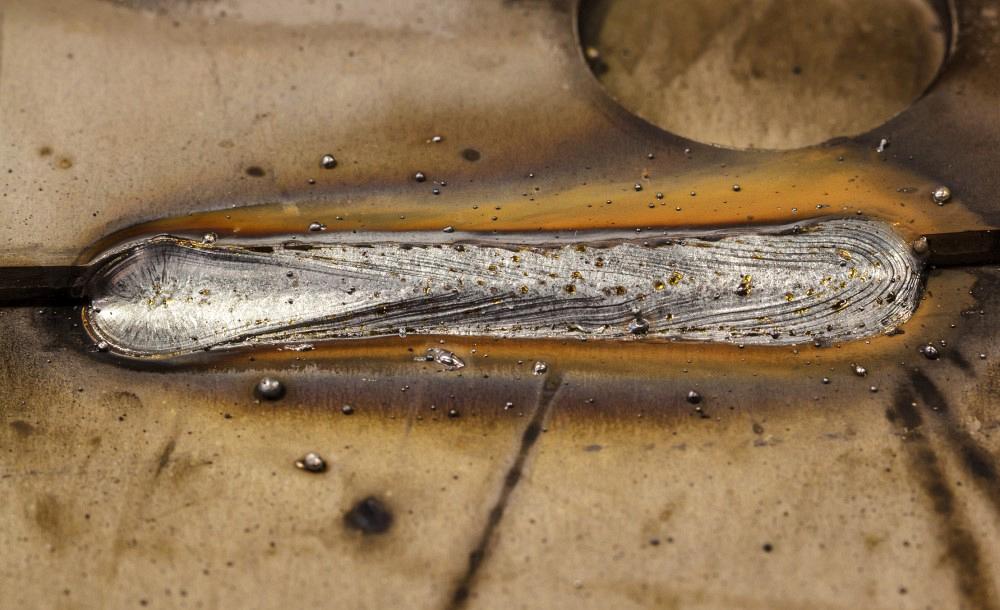
Utilizing filthy or wet filler products can present impurities into the weld, contributing to porosity issues. To reduce these usual reasons of porosity, thorough cleaning of base metals, proper protecting gas selection, and adherence to optimal welding parameters are important methods in accomplishing top notch, porosity-free welds.
Impact of Porosity on Weld Quality

The presence of porosity in welding can substantially jeopardize the architectural honesty and mechanical properties of welded joints. Porosity develops gaps within the weld steel, weakening its overall strength and load-bearing capability.
Welds with high porosity levels often tend to exhibit reduced impact stamina and decreased ability to deform plastically before fracturing. Porosity can hinder the weld's capacity to effectively transfer forces, leading to early weld failing and possible safety hazards in critical structures.
Best Practices for Porosity Avoidance
To improve the structural honesty and quality of bonded joints, what certain procedures can be implemented to lessen the event of porosity during the welding procedure? Porosity prevention in welding is important to guarantee the integrity and strength of the final weld. One efficient practice is appropriate cleaning of the base metal, eliminating any type of contaminants such as rust, check here oil, paint, or dampness that can bring about gas entrapment. Making sure that the welding devices remains in excellent condition, with clean consumables and suitable gas flow rates, can likewise substantially lower porosity. Additionally, keeping a steady arc and controlling the welding specifications, such as voltage, present, and take a trip rate, helps produce a consistent weld pool that minimizes the risk of gas entrapment. Utilizing the right welding method for the details product being welded, such as adjusting the welding angle and weapon position, can even more avoid porosity. Regular examination of welds and prompt remediation of any type of issues determined during the welding process are crucial techniques to stop porosity and produce high-grade welds.
Significance of Appropriate Welding Strategies
Executing appropriate welding strategies is critical in making certain the structural honesty and top quality of welded joints, building on the structure of effective porosity prevention steps. Welding strategies directly influence the total strength and durability of the bonded structure. One essential aspect of proper welding strategies is preserving the appropriate warm input. Excessive warmth can result in raised porosity because of the entrapment of gases in the weld swimming pool. Alternatively, not enough warmth may lead to incomplete blend, producing possible powerlessness in the joint. Clicking Here Furthermore, utilizing the proper welding parameters, such as voltage, present, and take a trip speed, is important for accomplishing sound welds with very little porosity.
Moreover, the selection of welding process, whether it be MIG, TIG, or stick welding, ought to line up with the specific demands of the project to guarantee optimum results. Correct cleaning and prep work of the base metal, along with selecting the ideal filler product, are also necessary elements of efficient welding methods. By sticking to these finest techniques, welders can minimize the threat of porosity development and generate high-quality, structurally audio welds.

Evaluating and Quality Assurance Procedures
Testing treatments are necessary to discover and protect against porosity in welding, making sure the toughness and toughness of the last product. Non-destructive moved here screening approaches such as ultrasonic screening, radiographic testing, and visual assessment are commonly used to recognize possible issues like porosity.
Post-weld assessments, on the other hand, examine the last weld for any kind of flaws, including porosity, and confirm that it meets defined criteria. Carrying out a comprehensive quality control plan that consists of extensive screening procedures and assessments is critical to lowering porosity issues and guaranteeing the total quality of welded joints.
Verdict
In final thought, porosity in welding can be a typical issue that affects the quality of welds. By determining the common reasons for porosity and applying ideal practices for avoidance, such as correct welding strategies and screening actions, welders can guarantee high quality and trusted welds. It is vital to prioritize avoidance approaches to reduce the incident of porosity and preserve the honesty of bonded frameworks.